Created to meet the needs of the preparation of official Mitsubishi bodies for rally raids, the composite and plastics department FASTER then developed its activities in the field of prototype for the automotive industry for the production of bodywork, structural parts or technical parts. The composite workshop was created in 1986 to take the advantage in rally raid when Faster embarks on the preparation of the bodies of 4×4 Mitsubishi soon winner on the African tracks. Faster then developed its activities in the field of competition and the prototype for the production of bodywork, structural part and automotive techniques for the industry. Mastering the various technologies used to implement monolithic and sandwich high-performance composite materials and techniques, Faster has long been able to offer tailored solutions to the different needs and expectations of its customers, whether for a single, prototype part or series. Integrated within the company running complete cars, the composite workshop has a perfect knowledge of the constraints and demands that the produced parts will have to undergo. Also Faster can, if necessary, accompany its customers throughout the development of the parts by making them profit from its long experience. This close collaboration, which is often implemented, makes it possible to achieve the initial objectives in terms of performance, price and time. In permanent link with the other Faster skills, the composite workshop is able to produce and deliver complex parts or subassemblies using different artisanal know-how and new technologies: Boilermaking, machining, harnesses, systems hydraulic and electronic, hybrid and electric engines.
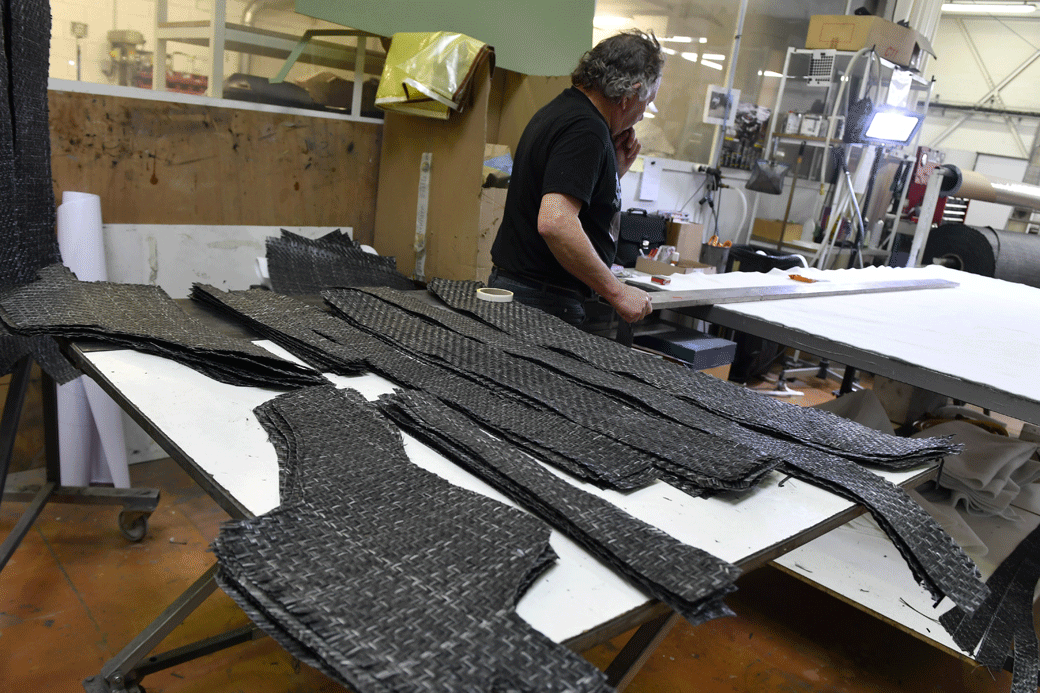
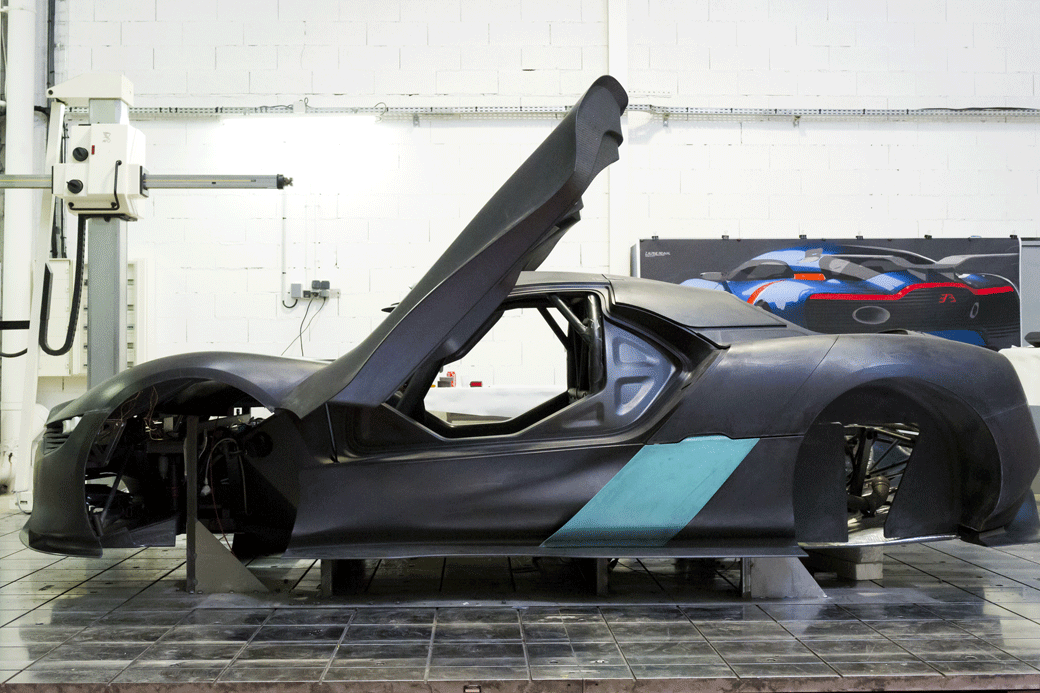
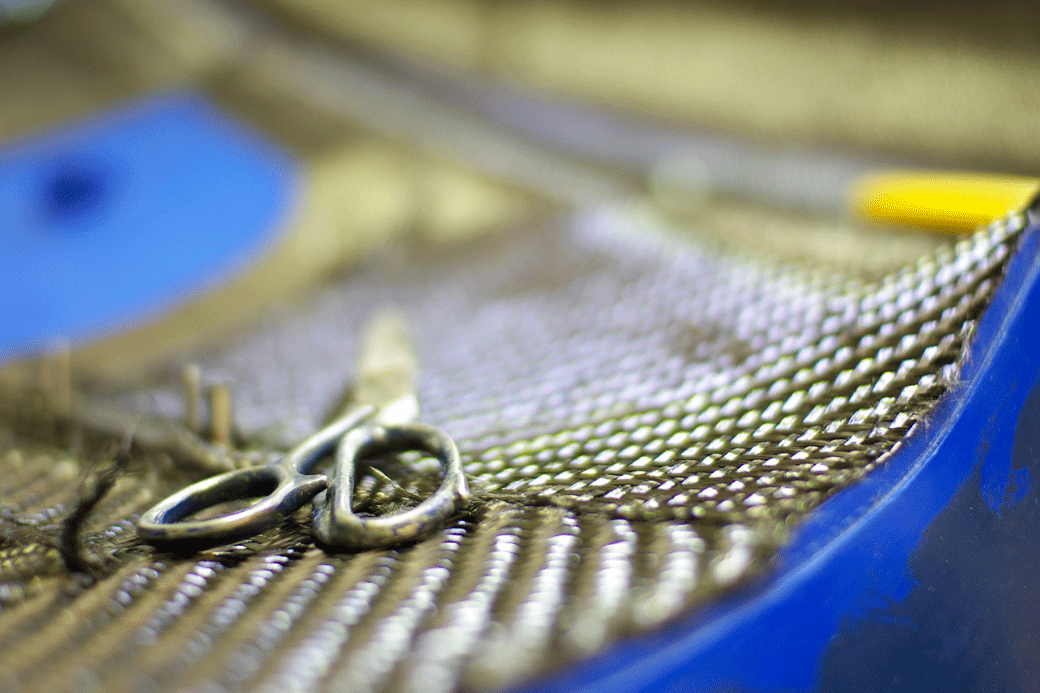
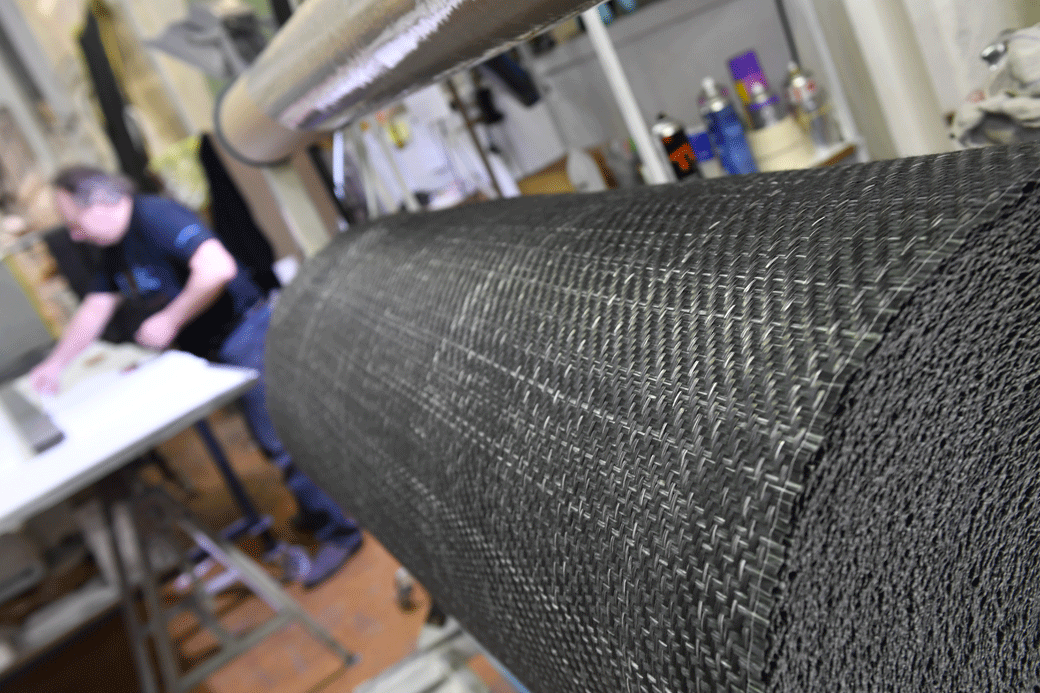
SKILLS
o Mastery of the different technologies for the implementation of technical composites with epoxy matrix: pre-impregnated, wet, wet vacuum, infusion, .. o Implementation of various common technical textiles: glass, carbon, kevlar, .. o Design and production of tools and parts o Modeling & modeling work o Production of single or small series prototype parts o Use of a digital cutter for pre-impregnated fabrics: optimal quality and repeatability for making parts small series. o Adjustment, assembly, assembly, gluing and riveting skills for the delivery of complex technical parts or complete subassemblies.
MEANS
o 1 cold room 30 m3 for storing the prepreg o 1 digital cutter LECTRA PROSPIN o 1 digitizing table A0: 1189 X 841 o 1 oven 250 ° C 30 m3 5000 X 3000 X 2000 o 1 oven 200 ° C 5.5 m3 2000 X 1750 X 1650 o 1 oven 350 ° C 1 m3 1000 X 1000 X 1000 o 2 vacuum pumps